Projects
10+ Years of Excellence – Innovative 3D Solutions for Confidential & Cutting-Edge Projects
With over 10 years of experience in the industry, we have successfully completed numerous high-precision 3D printing, scanning, and inspection projects across various sectors. While most of our work is protected under NDAs, we take pride in the cutting-edge solutions we’ve delivered for manufacturing, aerospace, automotive, medical, and industrial applications.
Here are some of the most interesting projects we’ve worked on:
🔹 Large-scale prototypes for product development
🔹 High-detail reverse engineering for legacy parts
🔹 Pipeline inspections using Creaform VXelements for structural integrity analysis
🔹 Organic object 3D scanning for art, archaeology, and medical research
Our commitment to precision, innovation, and confidentiality ensures that every project meets the highest industry standards.
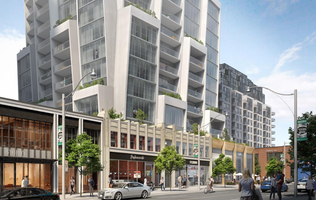
Qrint Precast Solution
Innovative Precast Mould Solutions for Modern Architecture
Welcome to Qrint Precast Solution, where we blend cutting-edge technology with architectural excellence to deliver top-notch precast mould solutions. Our expertise lies in transforming old designs into new, precise 3D models and 3D printing moulds for precast purposes.
Our Services3D Scanning and Modeling
At Qrint Studio, we specialize in scanning old tiles and producing new 3D drawings. Our advanced scanning technology ensures that every detail is captured, allowing us to create accurate and high-quality 3D models.
3D Printed Moulds
Using state-of-the-art 3D printing technology, we produce moulds for precast purposes. Our 3D printed moulds are designed to meet the highest standards of precision and durability, ensuring that your precast elements are of the best quality.
Featured Project: Studio Gang's Tower 1 Delisle Avenue
One of our notable projects includes providing precast mould solutions for Studio Gang's Tower at Yonge & St. Clair. This striking tower, designed by the renowned Studio Gang, features unique architectural elements that required precise and innovative mould solutions. Our team scanned the old tiles, produced new 3D drawings, and 3D printed the moulds to ensure the highest quality precast elements for this iconic structure2.
Why Choose Us?
Precision and Quality
: Our advanced technology ensures that every mould we produce meets the highest standards of precision and quality.
Innovation
: We stay at the forefront of technology, continuously improving our processes to deliver the best solutions for our clients.
Expertise
: With years of experience in the industry, our team has the knowledge and skills to handle even the most complex projects.

3D Modeling & Printing of Bighead Carp Embryonic Development for the Royal Ontario Museum
Bringing Science to Life – 3D Modeled & SLA Printed Bighead Carp Embryonic Stages for #ROMToronto
We had the privilege of collaborating with the Royal Ontario Museum's Ichthyology Department (#ROMToronto) on an exciting project involving the Bighead Carp's embryonic development. Using advanced 3D modeling software, we meticulously recreated the six stages of embryonic development, complete with detailed textures to enhance scientific accuracy.
Once the models were perfected digitally, we brought them to life using high-resolution SLA 3D printing, ensuring precision, clarity, and intricate detail. This project showcases our expertise in scientific visualization, museum displays, and educational models.
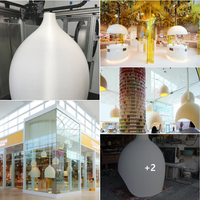
Large-Scale 3D Printed Light & Projector Pods for L’OCCITANE’s Interactive Display
Custom 3D Printed Light & Projector Pods – Precision Surface Finishing for LED & Interactive Projection
We had the privilege of working with L’OCCITANE on a large-scale 3D printing project, creating custom 2-foot light pods and 1-meter projector pods designed for LED lighting and interactive projection.
Using our high-precision large-format 3D printing technology, we crafted these pods with exceptional surface finishing, ensuring smooth diffusion for optimal lighting effects and seamless projection clarity. Our expertise in post-processing and material selection allowed us to achieve the perfect balance between durability, aesthetics, and functionality, bringing L’OCCITANE’s vision to life.
This project showcases our ability to deliver customized 3D-printed solutions for retail displays, experiential marketing, and interactive installations.
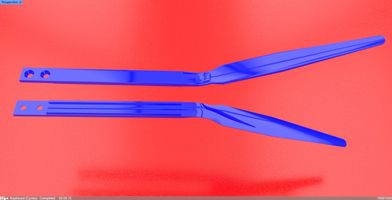
Molson Case Study
3D Printing Solution for Molson Brewery Packaging Line
Case Study: 3D Printing Solution for Molson Brewery Packaging Line
Client: JJDown for Molson Brewery
Industry: Beverage Packaging
Challenge: Molson Brewery faced a challenge with their packaging line machines. These machines relied on plastic fingers to help open boxes so the production line could insert beer bottles efficiently. Over time, these plastic fingers wore out, and the manufacturer no longer supplied replacements due to the machine model being outdated. These fingers had a unique characteristic: they possessed position memory, meaning they would return to a 30-degree bend regardless of how they were bent. This specific feature was crucial in guiding the beer bottles into the boxes accurately.
Solution: Qrint Studio stepped in to address this challenge with a cutting-edge 3D printing solution. Here's how they tackled the issue:
3D Modeling:
Qrint Studio created a precise 3D model of the plastic fingers, ensuring it matched the exact specifications required for the packaging line machine.They meticulously analyzed the original fingers to replicate their unique 30-degree position memory feature.
Material Selection:
Polypropylene was chosen as the material for the 3D-printed fingers. This material was selected for its durability and flexibility, making it ideal for the demanding environment of the packaging line.
3D Printing:
Utilizing advanced 3D printing technology, Qrint Studio produced high-quality replacement fingers that met the stringent requirements of the packaging line machine.The 3D printing process allowed for rapid production and ensured consistent quality across all replacement fingers.
Results:
Improved Efficiency:
The newly designed and printed plastic fingers seamlessly integrated into the packaging line, restoring its functionality and ensuring smooth operations.
Cost Savings:
By creating a custom solution, Molson Brewery avoided the need to invest in entirely new packaging line machines, resulting in significant cost savings.
Sustainability:
The use of 3D printing and durable materials extended the lifespan of the packaging line machines, reducing waste and supporting sustainability efforts.
Client Satisfaction:
JJDown and Molson Brewery were highly satisfied with the innovative solution provided by Qrint Studio, highlighting the studio's expertise in problem-solving and 3D printing technology.
Conclusion: Qrint Studio's 3D printing solution for Molson Brewery's packaging line machines showcased their ability to deliver tailored, high-quality solutions that meet specific client needs. By leveraging cutting-edge technology and material expertise, Qrint Studio successfully addressed a critical challenge, ensuring continued efficiency and productivity for Molson Brewery.